Superhuman Operator
Fehlerfrei bei Stückzahl Eins
Wie mit Augmented Reality die Montage von Spannsystemen im Sondermaschinenbau unterstützt wird

Holz gilt als nachhaltiger Rohstoff und steigende Einschlags- und Verarbeitungszahlen zeigen, dass er immer beliebter wird. Die Einsatzmöglichkeiten sind vielfältig, besonders intensiv wird der Naturstoff im Bauwesen, zum Beispiel für Fensterrahmen, Türen und Dachkonstruktionen genutzt. Ein weiterer großer Abnehmer ist die Möbelindustrie, deren Hauptwerkstoff das Holz ist. In beiden Industrien werden große Mengen Massivholz verarbeitet, meist aus Fichte, Kiefer oder Buche.
Bei der Verarbeitung des Massivholzes kommen verkettete Anlagensysteme zum Einsatz. Mit diesen wird das Holz vom Stamm bis zum Endprodukt verarbeitet. Es gibt nur eine Handvoll Unternehmen, die solche riesigen und hochkomplexen Sondermaschinen für die Massivholzbearbeitung bauen können. Eines der weltweit größten hat seinen Stammsitz im baden-württembergischen Tauberbischofsheim. Die Michael Weinig AG baut seit fast 80 Jahren Holzverarbeitungsmaschinen für große Möbelhersteller und die Bauindustrie.
„Ein Anlagensystem besteht aus Tausenden Einzelteilen in vielen Hundert Baugruppen. Es wird für jeden Einsatzzweck individuell gefertigt. Für die Fertigung der einzelnen Baugruppen setzen wir CNC-Maschinen ein.“
André Veith, Michael Weinig AG
„Ein Anlagensystem besteht aus Tausenden Einzelteilen in vielen Hundert Baugruppen. Es wird für jeden Einsatzzweck individuell gefertigt. Für die Fertigung der einzelnen Baugruppen setzen wir CNC-Maschinen ein,“ erklärt Andre Veith, Leitung Prozessmanagement & Infrastruktur / KVP bei der Michael Weinig AG.
Für die CNC-Bearbeitung werden Vorrichtungen benötigt, in die zu bearbeitende Bauteile eingespannt werden. Solche Spannsysteme können aus ganz verschiedenen Elementen, wie Anschlägen, Spanneisen, Spannpratzen oder Schraubstöcke bestehen. Sie werden für jedes Bauteil individuell zusammengestellt und manuell montiert. Diese Spannmittel von ganz unterschiedlicher Größe, Gewicht und Komplexität müssen absolut fehlerfrei und positionsgenau verschraubt werden. „Zwar haben wir von den Vorrichtungsteilen exakte 3D-Modelle, die unsere Mitarbeitenden auf Monitoren sehen, doch beim Zusammenbau sind Wissen und Erfahrung gefragt. Aktuell haben wir bereits alle vorgelagerten Prozesse wie z.B. virtueller Spannmittelaufbau, CAM-Programmierung, Simulation des realen NC-Codes auf einem digitalen Zwilling und sämtliche Verwaltungsprozesse der Spannmittel sowie Werkzeuge bereits digitalisiert. Jedoch fehlt uns noch der Übergang aus der „virtuellen“ in die „reale“ Welt im Vorrichtungsaufbau “ so Veith weiter. Trotzdem entstehen menschenverursachte Fehler beim Zusammenbau. Denn es erfolgt kein direkter Abgleich des physischen Vorrichtungsteils mit dem digitalen Modell. So kann es trotz sorgfältiger Arbeit zu Beschädigungen an der CNC-Maschine kommen, wenn die Spannvorrichtung falsch montiert wurde oder das Bauteil falsch eingespannt wird und es damit nicht exakt zum programmierten Ablauf der Maschine passt. Es kommt zur ungewollten Kollision im Vorschub oder Eilgang. Im schlimmsten Fall ist Maschine so schwer beschädigt, dass sie ganz ausfällt und repariert werden muss. „Ein einziger Stillstand der CNC-Maschine kann schnell mit einem fünfstelligen Betrag zu Buche schlagen,“ beschreibt Veith das Problem.
Eine Lösung dafür hatten die Wissenschaftler am Fraunhofer IFF bereits vor einigen Jahren für einen anderen Sondermaschinenhersteller entwickelt. Das Unternehmen Kolbus GmbH & Co. KG stellt im ostwestfälischen Rahden Maschinen zur Buchdeckel- und Packmittelfertigung im Sondermaschinenbau her und stand vor einer ähnlichen Herausforderung wie die Michael Weinig AG. Hier ging es ebenfalls um individuelle Montageprozesse für Spannsysteme.
„Wir haben eine technische Lösung entwickelt, bei der das Fachpersonal von einem digitalen Assistenzsystem unterstützt wird.“
Steffen Sauer, Fraunhofer IFF

„Wir haben eine technische Lösung entwickelt, bei der das Fachpersonal von einem digitalen Assistenzsystem unterstützt wird. Ein Kamerabild nimmt den Arbeitsbereich auf. Über dieses Bild wird mittels Augmented Reality das 3D-Modell der Baugruppe gelegt. Der Mitarbeitende kann nun in Echtzeit die Lage und Richtigkeit der einzelnen Bauteile bereits bei der Montage überprüfen,“ beschreibt Steffen Sauer, Projektleiter am Fraunhofer IFF die technische Lösung. Das System hat eine Abweichungstoleranz von nur 0,3 mm. Jedes Bauteil wird einzeln eingeblendet und bei richtigem Sitz an der Baugruppe quittiert, bevor es zum nächsten Einzelteil weitergeht. Damit werden menschliche Fehler in der Konstruktion der Vorrichtung für die CNC-Maschine nahezu ausgeschlossen. „Seit dem Ersteinsatz bei Kolbus hat es keine menschenverursachten Kollisionen der dortigen CNC-Maschine mehr gegeben. Außerdem funktioniert dieses System sehr intuitiv, der Anlernaufwand ist gering,“ berichtet Sauer. Diese Vorteile überzeugte die Michael Weinig AG, ein solches individuelles Assistenzsystem beim Fraunhofer IFF in Auftrag zu geben.
Kolbus hat zwischenzeitlich so viel Erfahrung mit dem Assistenzsystem gesammelt, dass deren Wissen um die Arbeitsplatzgestaltung mit in die Lösung für die Michael Weinig AG eingeflossen ist. „Wir haben ein Joint Venture mit Kolbus aufgesetzt. Sie bringen Praxiserfahrung bei der Arbeitsplatzgestaltung ein und wir entwickeln die passende Software für die Michael Weinig AG“, so der IFF-Wissenschaftler weiter.
Besonders produktiv entwickelte sich auch die Zusammenarbeit mit der Fa. Pimpel aus Österreich. Mit der von ihnen entwickelten Software CHECKitB4 sind sie bei der Michael Weinig AG für die CAD/CAM-Datenbereitstellung verantwortlich. In CHECKitB4 können die digitalen Zwillinge (3D Solid inkl. Kinematik Achsen) von Spanneisen, Spannpratzen und Schraubstöcke als auch Werkzeugmaschinen 1:1 abgebildet werden. Dadurch kann das Werkstücksetup für die jeweilige Maschine sehr einfach erstellt und auf Machbarkeit geprüft werden. Fasziniert von den Möglichkeiten der durchgehenden digitalen Kette von Konstruktion bis Bearbeitung entwickelte Pimpel in enger Abstimmung mit dem Fraunhofer IFF ihre Software weiter. So ist es nun möglich, mit minimalem Vorbereitungsaufwand aus der CAD/CAM-Software die Montageanweisungen zu exportieren und direkt in die Assistenzsoftware zu laden.
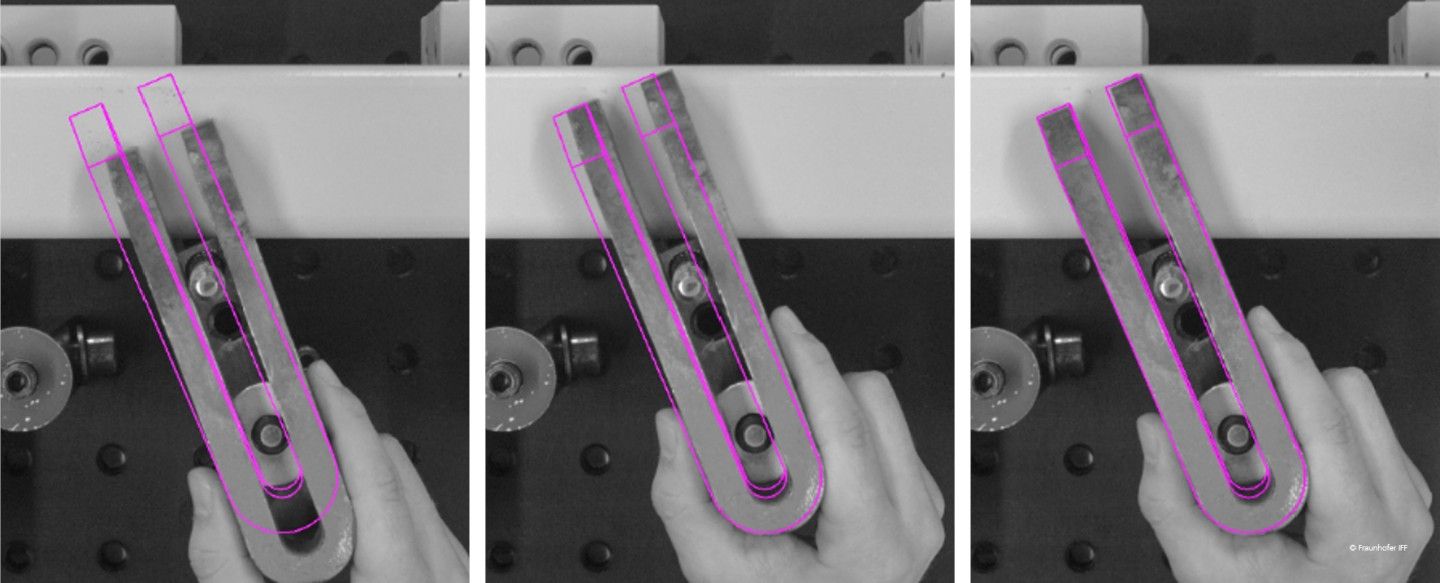
Mit dem Assistenzsystem wird der Mensch in der Fertigung befähigt, komplexe Arbeitsabläufe schnell und einfach zu erlernen. Die manuelle Fertigung wird um einen in Echtzeit parallellaufenden digitalen Prozess ergänzt. Damit werden die Vorteile beider Welten – höchst individuelle händische Fertigung und klar definierte, fehlerfreie digitale Prozesse – zusammengeführt. Dem Menschen kommen hier neben der reinen Montage der Bauteilgruppe auch steuernde Aufgaben im Prozessablauf zu. Der Mensch bleibt zentral, trifft die Entscheidungen – und wird durch das Assistenzsystem wirksam unterstützt.
Die assistierte Spannmittelmontage hat noch einen weiteren Vorteil: Bisher muss die Maschine bei der Erstbearbeitung eines Teiles das Bearbeitungsprogramm im Einzelschrittmodus durchlaufen. Dies wird durchgehend von kundigem Fachpersonal überwacht. Ein aufwendiger Arbeitsschritt, der nicht wertschöpfend und ineffizient ist. Dieses zeitaufwändige Einfahren der CNC-Maschine entfällt nun komplett. Die Maschine kann nach Einbau des Spannsystems sofort mit dem zu bearbeitenden Bauteil bestückt werden. Die Daten werden in Echtzeit aktualisiert und stehen für die nachgelagerten Produktionsprozesse zur Verfügung.
Gerade in hochindividualisierten Montageprozessen wie dem Sondermaschinenbau sind Wissen und Erfahrung der Mitarbeitenden oft ausschlaggebend für den wirtschaftlichen Erfolg eines Unternehmens. Die assistierte Spannmittelmontage hilft dabei, häufig wechselnde Montageprozesse schnell und intuitiv zu lernen. Auch nicht oder gering für diese Aufgabe qualifizierte Mitarbeitende können mithilfe der Assistenz schnell in diese Arbeit eingelernt werden. Das ermöglicht ein breiteres Einsatzgebiet der Menschen und schafft Flexibilität in der Personalplanung. All dies erhöht die Attraktivität von Fabrikarbeitsplätzen in Zeiten knapper Fachkräfte.
Die assistierte Spannmittelmontage ist bei der Michael Weinig AG ein voller Erfolg. „Wir haben zunächst zwei Arbeitsplätze mit dem neuen System ausgestattet. Einen weiteren Arbeitsplatz haben wir als Backup unverändert gelassen,“ sagt Andre Veith und fügt hinzu: „Aber jetzt will da keiner mehr arbeiten. Alle wollen nur noch die neue Technologie nutzen. Somit ist klar, dass dies nicht der letzte Arbeitsplatz des IFF im Hause Weinig ist, weitere Einsatzmöglichkeiten werden bereits intern erörtert. Aktuell prüfen wir, ob wir die Technologie auch im Maschinenraum bzw. im Bereich der Paletten Spannung bei Großmaschinen integrieren können.“